Chapter 3. How to Use a Lathe
Drilling and Boring Bar
Making of a Hole with a Lathe
When we use a lathe, we can make an accurate hole. If the hole has a small
diameter, a drill is used for the processing. On the otherhand, if the
hole has a big diameter or it is needed the accurate diameter and roughness,
a special cutting tool for a lathe, called a boring bar, is used.
Using of a Drill
It is not difficult to set a drill into a drill chuck of a lathe and push
it to a material. But a thin drill is broken easily by an unreasonable
force. Then, scraps of the material should not keep in the slot of the
drill. We should give a cutting oil, and discharge the scraps briskly.
When there is a protruding at the center of a material, the drilling hole turns in the material. Then we usually use a center drill, whichi has a strong rigidty, and make a mark before using of the normal drill.
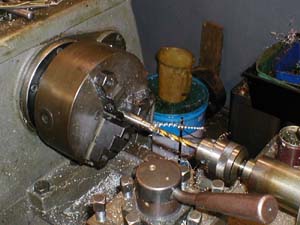
Fig.1, Drilling
|
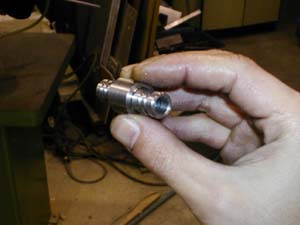
Fig.2, Completed Part
|
Using of a Boring Bar
A boring bar is used in the cutting of an inner suface. It can make the
hole, which has a big diameter, which is needed an accurate diameter, and
which is needed a high surface roughness.
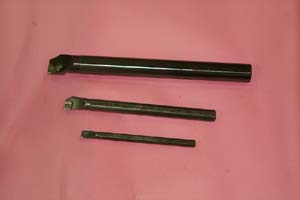
Fig.3, Boring Bars
|
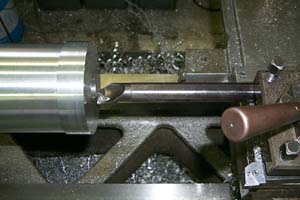
Fig.4, Setting of a Boring Bar
|
Why is the boring processing difficult?
The boring processing is said that it is difficult. The reasons are in
follows.
(1) We are hard to see the processing surface.
(2) The scraps are kept in the hole. When the scraps are kept, the surface
cannot be finished to high roughness.
(3) Because we cannnot see the bottom of a deep hole, it is hard to stop the boring bar at the bottom location. We must depend the scale of thelathe and the sound.
(4) Especially the case of a small hole, the backside of the boring bar touches a material. We must set the hight of the edge suitably.
(5) Because a boring bar is long, the tool has vibrations easily. It is
depended on the rigidty of the boring bar. |
Actual Boring Processing
Follows phptographs introduce the actual boring processing of a mechanical part of a fish robot. The material is aluminum alloy (JIS A2017). The size is 118 mm of outer diameter and 191 mm of length. The hole is 103 mm of inner diameter and 186 mm of depth. The part is waterproofed by an O-ring, the the inner surface is needed to have a high roughness.
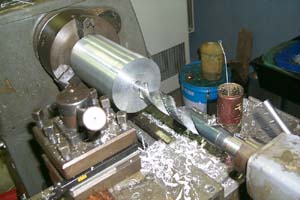
(1) An under hole is made with a drill.
|
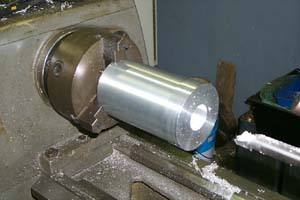
(2) The hole is spreaded with a boring bar.
|
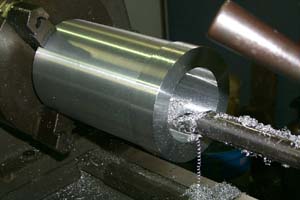
(3) The edge must not attack to the bottom surface.
|
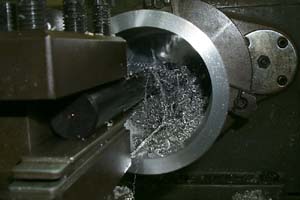
(4) It is too hard to see the inner surface by scraps.
|
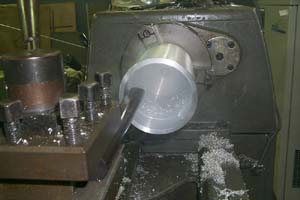
(5) The diameter becomes big. The cutting of the thin material is too hard.
|
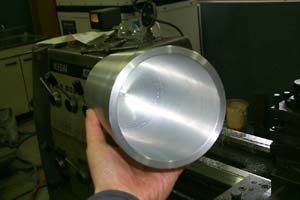
(6) The boring processing is finished. It has a beautiful surface.
|
Fig.5, Actual Boring Processing
Boring Processing of a Thin Pipe
The cutting of a thin material is too hard. Because the material has vibrations
and it has a bad roughness. In such cases, generally the rotating speed
must be low. Stillmore, when the vibrations cannot be stopped, it is better
to roll a long rubber belt around the material. Figure 6 shows the boring
processing of a thin material with the rolled rubber belt.
Fig.6, The Boring Processing of a Thin Pipe
|
[ Metal Working TOP ]
[ Hirata HOME ]
[ Power and Energy Engineering Division ]
[ NMRI HOME ]
|