Heat Exchangers
In order to get a smaller size and low production cost, a simple moving-tube-type heat exchanger was adopted. A couple of inner-outer tube was located in the central axis of the displacer. The inner tube of heater, and the inner and outer tube of cooler were easily assembled (see the belows photos). It then is considered that this type of heat exchanger obtains pretty lower production cost than that of previous multi-tube type heat exchangers. In addition, the new type heat exchanger needs little welding.
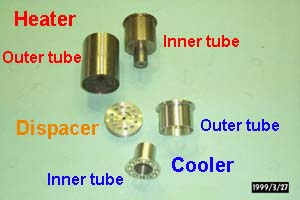
In the case of design for a cooler, the calculated result of the heat transfer was not enough high performance. In order to get sufficiently rejected heat, large amount of cooling water is required. Supplying sufficient water was possible in the experiment, though it might not be practical
The shape of a displacer and its assembling method affect a size of a regenerator. Wire gauze made of brass (#100, diameter of 0.1 mm, 70 sheets) was used as a regenerator matrix.
|