講義ノート:もの作りのための機械設計工学
第3章 機械の強度と設計
3.1 機械加工の種類と特徴
機械加工は,大学や工業高校の機械実習工場における機械加工から,機械製品を生産のため機械加工に至るまで様々である。その加工法は設備の規模などによって様々であるが,以下では機械加工の最も基本となる単品製作の切削加工を中心に紹介する。なお,さらに詳細な機械加工については以下のホームページを参考にしていただきたい。
「機械加工の基礎知識」のページへ
3.1.1 機械加工法
機械加工法は,切削加工,付加加工および塑性加工の3種類に大きく分けられる。図3.1に示す切削加工は,材料から不要な部分を削りとる加工であり,代表的な加工として旋盤加工やフライス加工,ドリル加工などがある。切削加工は,製作コストや製作時間の観点から大量生産には適していない。しかし,切削加工だけでも,かなり複雑な機械を作ることができるので,最も基本となる加工法と言ってよい。付加加工は,材料に別の材料を付け加える加工であり,代表的な加工として図3.2に示す溶接やロウ付けがある。塑性加工は,材料を削ったり,新たな材料を付け加えたりすることなく,材料の展延性を利用した加工である。塑性加工の代表的な加工として曲げ加工や絞り加工などのプレス加工(図3.3)がある。
|
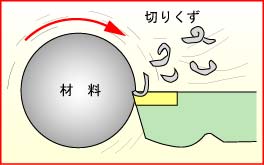
図3.1 旋盤加工(切削加工の例)
|
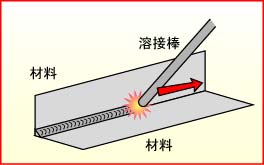
図3.2 溶接加工(付加加工の例)
|
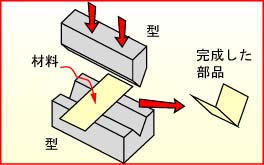
図3.3 プレス加工(塑性加工の例)
|
どのような加工法を用いるかは機械加工の設備や製作する機械の数などによって異なる。また,それぞれの加工法にはそれぞれに適した部品形状がある。機械設計においては,これから設計する機械がどのような加工法で作られるのかをしっかりと把握しておかなければならない。
大量生産と単品生産
実際の機械製品を作る場合,多くの切り屑を出すことは好ましくない。材料コストが増え,さらに加工時間も増えるためである。そのため,大量生産品を作る場合には,切削加工よりもプレス加工を用いることが多い。しかし,プレス加工は,一対の型に対して一種類の形状の部品しか作ることができないので,実験装置などの単品製作には適していない。一方,切削加工は旋盤とフライス盤があれば,様々な形状の部品を作ることができるので,実験装置などの単品製作に適している。
|
3.1.2 旋盤加工と設計
(1) 旋盤加工の概要
図3.4(a)に示す旋盤は,円柱状の材料を回して,それにバイトと呼ばれる刃ものを当てて,材料を削る工作機械である。図3.4(b)に示すように,材料を旋盤のチャックに固定して回転させる。そして,バイトの位置を前後方向および左右方向に動かし,バイトの先端を材料に当てて削っていく。
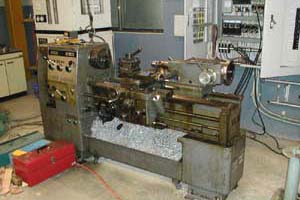
(a) 旋盤の外観
|
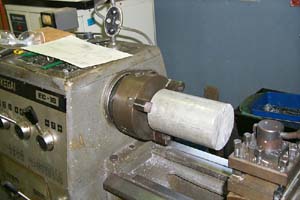
(b) 材料の固定
|
図3.4 旋盤
(2) バイトの形状と旋盤加工
図3.5は旋盤加工で使われる代表的なバイトである。図3.5(a)は旋盤加工で最もよく使われる右片刃バイトであり,図3.6に示すように円柱材料の外面(曲面)と端面(平面)を削ることができる。旋盤加工において,右片刃バイトは最も扱いやすいので,右片刃バイトだけで加工できる形状は最も加工しやすい形状である。したがって,機械設計においては,可能な限り右片刃バイトだけで加工できる形状とするのが望ましい。なお,普通の旋盤は材料の左側をチャックで固定するので,右片刃バイトでは材料の右側の端面しか加工できない。
図3.5(b)の突切りバイトは,材料を切り落としたり,円周方向の溝を削るのに使う。先端部分が細く,壊れやすいので,右片刃バイトと比べてやや扱いにくい。
図3.5(c)の中ぐりバイトは,円筒形状の内面を削る際に使用する。例えば,ドリルでは加工できないような大きい穴,あるいは精度が必要で滑らかな加工面に仕上げる穴の加工などである。
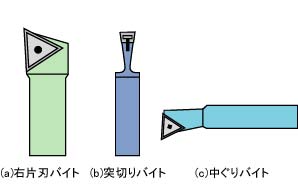
図3.5 旋盤加工に用いる代表的なバイト
|
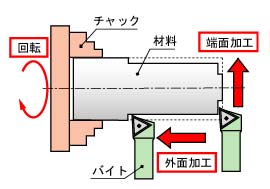
図3.6 右片刃バイトを使った旋盤加工
|
(3) 加工しやすい形状と加工しにくい形状
図3.7は旋盤加工で作りやすい形状と作るにくい形状の例を示している。突切りバイトを使用する場合,溝の幅が細く,溝が深くなるほど加工しにくくなる。また,中ぐりバイトを使う場合,バイトの高さが合ってさえいれば,貫通する穴を加工するのはそれほど難しくない。しかし,貫通していない内面の中ぐり加工は,加工中に内部を見ることができないため,やや難しくなる。さらに,直径が小さい場合(10 mm以下)や深い穴の場合の中ぐり加工は著しく難しくなる。もちろん,図3.7(c)に示すような物理的に加工できない形状もある。そのような場合は,機械設計時に部品を分割するなどの工夫が必要である。
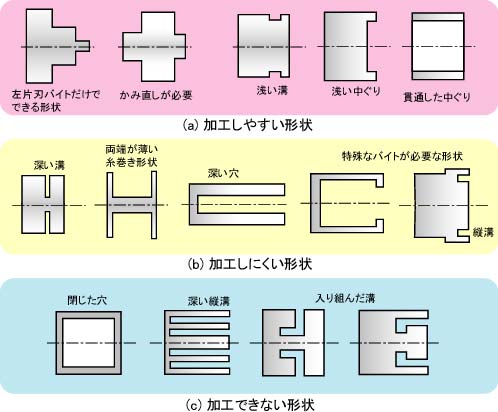
図3.7 加工しやすい形状と加工しにくい形状
(4) 特殊な形状の加工
部品の形状が複雑な場合や通常の旋盤加工では製作が難しい場合,ジグ(加工を補助するための道具)を使う。ジグは製作者によって作られるのが普通であるが,機械設計者も加工方法についてしっかりと考えておきたい。いずれにしても,旋盤では「丸い形状」しか作ることができない。設計者は以上のような旋盤の使い方をしっかりと把握しておかなければ,機械設計において適切な部品の形状を決めることができない。
3.1.3 フライス加工と設計
(1) フライス盤の概要
フライス盤とは,回転している工具に,バイス(万力)に固定した材料を当てて加工する工作機械である。フライス盤には回転軸が鉛直方向にある縦フライス盤と回転軸が水平方向にある横フライス盤とがある。一般に,横フライス盤は,加工速度が速いという特徴がある。しかし,工具の付け替えがやや面倒であり,製作できる部品の形状に限度がある。以下,汎用性に優れた縦フライス盤(図3.11)について説明する。
|
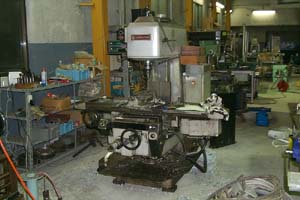
図3.11 縦フライス盤
|
(2) エンドミル
図3.12に示すエンドミルは,フライス加工の代表的な工具である。回転しているエンドミルを材料に当てて,左右方向または前後方向に材料を動かすことで平面を作るのが基本的な使い方である。エンドミルは,先端の面と側面が「刃」になっている。これを使用することで様々な形状の部品を製作できる。
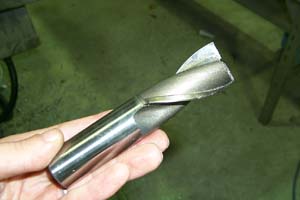
(a) エンドミル
|
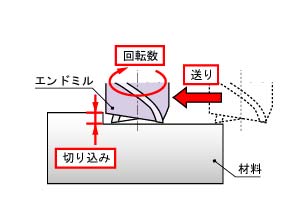
(b) エンドミルによる切削加工
|
図3.12 エンドミル
(3) 機械設計における注意点
一般に,フライス加工は旋盤加工と比べて加工速度が遅い。したがって,部品を製作する際にフライス盤と旋盤のどちらでも使うことができるのであれば,旋盤を使う設計とするのが望ましい(図3.13)。また,フライス加工で製作する部品は,バイスに固定しやすい形状とするのがよい(図3.14)。
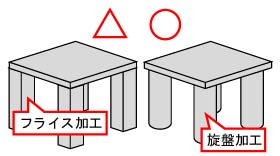
図3.13 フライス加工と旋盤加工
|
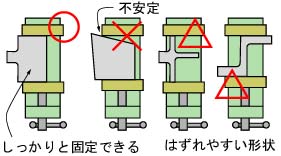
図3.14 バイスに固定しやすい形状
|
フライス加工の実際
フライス盤を使うことで,様々な形状の部品を作ることができる。その制作手順については別のページで紹介することとし,最終的に完成したいくつかの部品を紹介する。図3.15は,図1.12の魚ロボットの部品である。エンドミルを使って複雑な形状に仕上げている。図3.16は,同魚ロボットの背骨であり,フライス盤を使って製作したいくつかの部品が組み合わされている。ほとんどの部品は直方体に近い簡単な形状である。
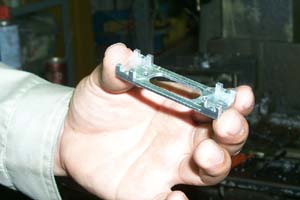
図3.15 魚ロボットの部品
|
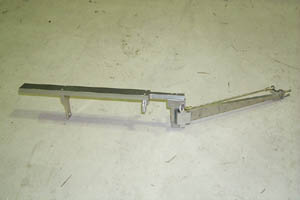
図3.16 魚ロボットの背骨
|
|
3.1.4 ドリル加工と設計
ドリルは,穴あけ加工に使用する工具であり,機械加工で最もよく使われる工具の一つである(図3.17)。先端部分が「刃」になっており,ドリルは直径1 mm以下のものから40 mm以上のものまで様々なものが市販されている。金属加工に用いられるドリルは,先端の角度が90度または120度になっているのが普通である。
|
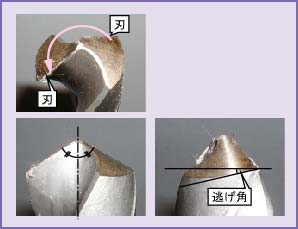
図3.17 ドリル
|
ドリル加工における機械設計の注意点として以下のことがあげられる(図3.18)。
(a) 細いドリル(直径2 mm以下)は折れやすいので,できる限り使わないようにする。
(b) 穴が深くなると加工が難しくなるので,必要以上に深い穴を指定しない。
(c) 穴の深さに精度を求めるのは難しい。板材のぎりぎりで穴を止めるなどの加工は望ましくない。
(d) ドリルの長さ以上に深い位置や他の部分が干渉する場所など,ドリル加工ができない場所がある。
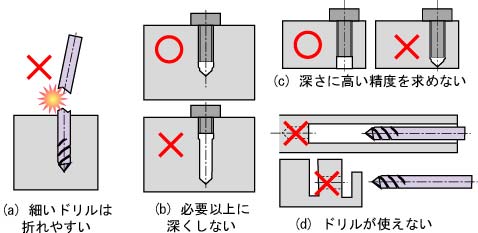
図3.18 ドリル加工における機械設計の注意点
ドリル加工と機械製図
機械製図において,ドリル加工は「キリ」と表される(図3.19(a)参照)。すなわち,「5キリ」とあれば直径5 mmのドリルを使って穴をあけることになる。また,穴の深さを指定する場合,「5キリ深サ10」などと表示する。この場合,ドリル先端のテーパ部は含まれないので注意する(図3.19(b)参照)。
|
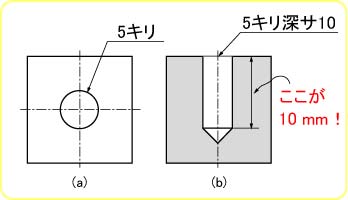
図3.19 ドリル加工と機械製図
|
3.1.5 溶接加工と設計
溶接とは,金属材料同士の接合部を高温の熱によって溶かして接合する加工である。鉄鋼材料の溶接法として最もよく使われるのが,図3.20(a)に示すアーク溶接である。ステンレス鋼やアルミニウム合金の溶接には,図3.20(b)のTIG溶接などが用いられる。図3.20(c),(d)はTIG溶接でスターリングエンジンの部品を製作した例である。
一般に,溶接加工は,熱を与えることで材料が変形してしまうため,切削加工と比べて正確な寸法に仕上げることが難しい。製作者の技能によるが,一般には精度が高い部品を製作する場合に溶接加工を用いるのは好ましくない。
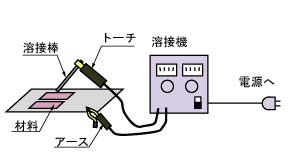
(a) アーク溶接機の構成
|
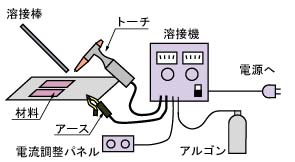
(b) TIG溶接機の構成
|
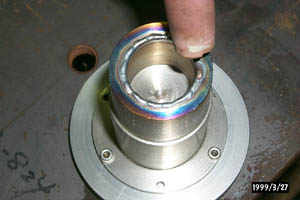
(c) TIG溶接で製作した部品
|
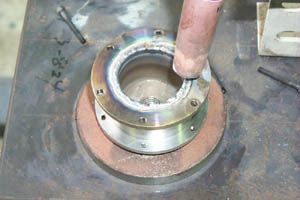
(d) TIG溶接で製作した部品
|
図3.20 溶接加工
ロウ付け
ロウ付けは,溶接に類する接合法であり,材料そのものを溶かすことなく,ロウ(ハンダや銀ロウ)だけを溶かし,ロウと金属材料とを接合させて,金属材料同士を接合する(図3.21)。ロウ付けは,溶接と比べて加工時の温度が低く,手軽な加工であるが,ロウと金属材料との相性などに問題が生じることがある。
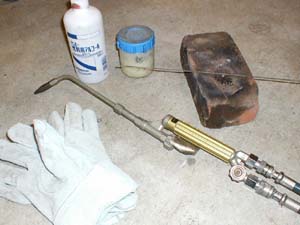
(a) ロウ付けに必要な用具
|
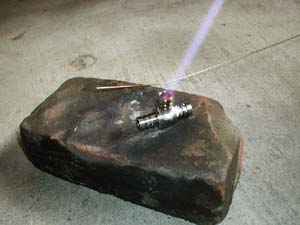
(b) ロウ付けをしている部品
|
図3.21 ロウ付け
|
もっと詳しい「機械加工の基礎知識」のページへ
|