講義ノート:もの作りのための機械設計工学
第9章 機械システム設計
9.2 実験用小型スターリングエンジンの設計
スターリングエンジンは高熱効率性,燃料の多様性及び低公害性等の優れた特徴を持つ動力源であるが,未だ民生レベルでの実用域に達していないのが現状である。スターリングエンジンの実用化を阻む問題点として,多数の伝熱管を溶接して製作される熱交換器の製造コストが高いことおよびエンジン重量当たりの出力が小さいことがあげられる。本節で紹介する実験用小型スターリングエンジン(図9.3)は,それらの解決策を見出すことを目的とし,簡略化した熱交換器の採用や小型化のための工夫を施したスターリングエンジンである。
50W級スターリングエンジン「Mini-Ecoboy」
|
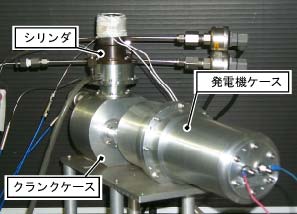
図9.3 実験用小型スターリングエンジン
|
9.2.1 エネルギーの流れ
スターリングエンジンを設計するに当たって,最初にエネルギーの流れを把握しておく必要がある。図9.4は,スターリングエンジンにおけるエネルギーの流れを簡易的に表している。高温熱源から与えられる全熱量Qin(熱入力)がエンジンの出力軸から取り出される出力Ls(軸出力)に変換される過程で,様々な熱損失が生じていることがわかる。スターリングエンジンの熱交換器やピストン駆動機構を設計する際には,このようなエネルギーの流れを把握した後,必要とされる交換熱量などの設計計算を進めることとなる。
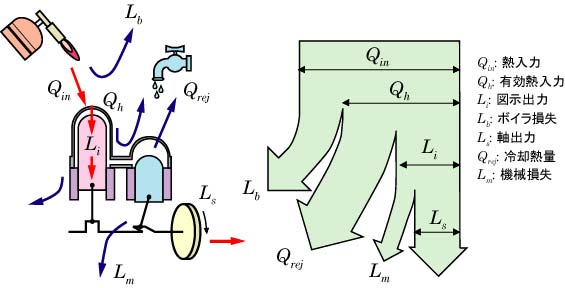
図9.4 エネルギーの流れ
エネルギーフローの詳細
図9.4において,熱入力Qinは高温熱源から与えられる全熱量である。燃焼ガス加熱では燃料の発熱量と流量,電気ヒータ加熱では電圧と電流との積で求められる。有効熱入力Qhは,熱入力Qinからボイラ損失Lbを差し引いた熱量であり,実際にエンジン内に取り込まれる熱量である。ボイラ損失は高温熱源から大気へ放出する熱損失であり,実用形エンジンでは燃焼器や空気予熱機器(排ガスの熱により燃焼用の空気を加熱する装置)によりこの熱損失を減らしている。有効熱入力Qhは,冷却熱量Qrejと図示出力Liとに変換される。冷却熱量Qrejには,作動ガスを冷やすための熱量(圧縮仕事)や次項で述べる熱伝導による損失が含まれており,概ね冷却器(クーラ)での交換熱量に等しくなる。図9.4からわかるように,冷却熱量Qrejが小さいほど熱入力を少なくすることができ,高効率が得られる。図示出力Liは,作動ガスがピストンに作用する出力であり,作動ガスの瞬時圧力P,エンジン内瞬時容積Vおよび回転数nから求められる。図示出力Liは,機械損失Lmを差し引いた後,軸出力Lsとなる。機械損失Lmは,ピストンとシリンダとの間の摩擦やピストン駆動機構部での摩擦による損失である。軸出力Lsは,平均エンジントルクTqmと回転数nから求められる。
|
9.2.2 出力試算
通常のエンジン設計では,最初に目標とする出力を決める。出力の試算には様々な方法があるが,本実験用小型スターリングエンジンにおいては,今までに開発された多種エンジンの実測データに基づく性能予測法を用いた。本性能予測法は,圧力,温度,容積および作動ガスの種類などの影響を整理した実験式により,エンジン回転数や軸出力を求める計算法である。
エンジンを小型化するためには,高いエンジン回転数で運転させることが必要である。本予測法によると,パワーピストンの行程容積が小さいほど高いエンジン回転数が得られる。本予測法による計算結果および後述する熱交換器やピストン駆動機構の構造を検討した結果から,エンジンのシリンダ径を36 mm,ストロークを10 mmとし,目標軸出力を50 Wとした(表9.1)。図9.5は本性能予測法による計算結果の一例である。これより,作動ガスにヘリウムを使用し,平均圧力を0.8 MPaとした場合,エンジン回転数が約4000 rpmで目標軸出力である50 Wが得られることがわかる。
簡易性能予測法の提案
スターリングエンジンの簡易性能予測法
|
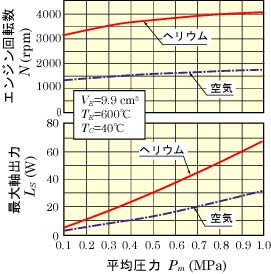
図9.5 性能予測法による計算結果
|
表9.1 エンジン仕様および目標性能
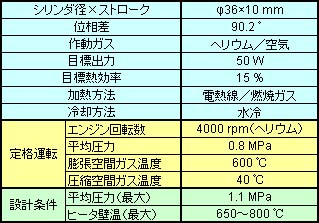
9.2.3 基本設計
スターリングエンジンの主な構成要素としては,ヒータ,クーラおよび再生器で構成される熱交換器,2つのピストンを動かすための駆動機構並びに出力の取り出し(本エンジンの場合は発電機)がある。これらの詳細寸法を決定するためには,各要素の性能特性を試算したり,あるいは検討したりすると同時に,エンジン全体の構造を検討する必要がある。
図9.6は,最終的に試作したエンジンの構造を示している。本エンジンはディスプレーサとパワーピストンとを直線上に配置し,さらに,再生器をディスプレーサに内蔵することでエンジン内の空間を有効に利用でき,エンジンの小型化を図っている。
ヒータおよびクーラには,簡易的な熱交換器を採用した。図1.9に示したような模型スターリングエンジンと比べるとかなり複雑であるが,数十〜数百本もの伝熱管を配置した一般の実用形スターリングエンジンの熱交換器と比べると大幅なコスト低減が可能であると考えられる。
ピストン駆動機構を検討するに当たって,高回転で運転するエンジンではバランス性が最も重要であると考え,優れたバランス性を有するロンビック機構(図6.28,図6.29)を採用している。
|
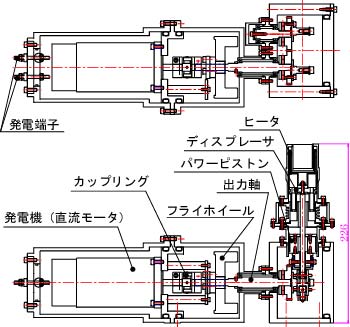
図9.6 実験用小型スターリングエンジンの構造
|
9.2.4 構成要素の設計
以下,エンジン全体の構造を検討するのと同時に行った,熱交換器やピストン駆動機構などの各構成要素の設計について説明する。
(1) ヒータ
本エンジンのヒータは,ディスプレーサ上端のヒータ内管とシリンダと一体構造としたヒータ外管から構成される(図9.7)。作動ガスは内管および外管の間の環状部を流れる。ヒータの設計においては,ヒータ壁と作動ガスとの間の伝熱計算や高温かつ高圧に耐えられるヒータ外管の肉厚を求める強度計算が必要となる(図2.7参照)。これらの計算を行うには,熱力学および材料力学の知識が必要である。
|
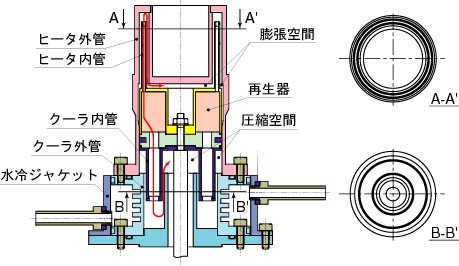
図9.7 熱交換器の構造
|
図9.8は,試作したヒータに対する計算結果の一例であり,内管と外管との隙間CLをパラメータとし,エンジン内平均圧力Pmとヒータ管温度Twとの関係を示している。これより、CL=0.5 mm、Pm=0.8 MPaにおいて,膨張空間内ガス温度TEを600℃にするためには,ヒータ管を660℃まで加熱する必要があることがわかる。また,伝熱性能は、隙間CLが小さいほど向上する。しかし,この隙間は,内管と外管との接触を避けるため,ピストン駆動機構の組立精度を考慮して決定する必要がある。
|
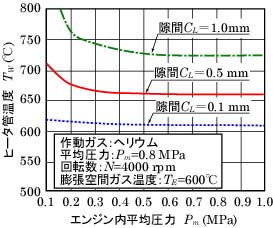
図9.8 ヒータの設計計算例
|
(2) クーラ
クーラは,エンジン内のガス温度を適切に保つために重要な役割を果たす。クーラの設計計算では,管内および管外熱伝達を計算し,冷却熱量などを求めた(図9.9)。その結果,図9.6に示したクーラ形状では,冷却水側の伝熱面積が不足し,設定した圧縮空間内ガス温度(40 ℃)を維持するのは難しいことが確認された。十分な冷却熱量を得るためには,多量の冷却水流量が必要になる。
|
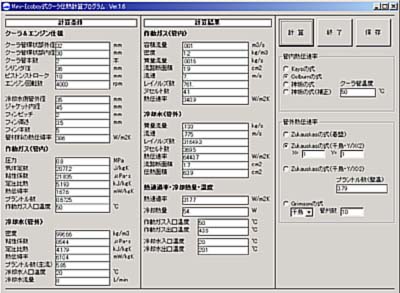
図9.9 クーラの設計計算画面
(画面をクリックすると大きい画像が表示されます)
|
(3) 再生器
再生器は,ヒータとクーラの間に取り付けられる蓄熱式熱交換器であり,スターリングエンジンの熱効率を向上させるために重要な構成要素である。すなわち,再生器が正しく機能しないと,ヒータに取り入れられた熱量の一部が無駄に捨てられることとなり,エンジン性能が低下すると同時にヒータやクーラへの負担が大きくなる。
本エンジンの再生器寸法は,ディスプレーサ形状および製作上の制約から設定され,外径34 mm,内径13 mm,長さ17.5 mmとした(図9.10)。再生器空間には,黄銅製のメッシュ(#100,線径0.1mm,70枚)を挿入している。通常,再生器寸法が大きくなると,伝熱性能は向上するが,圧力損失(作動ガスが流れることによって生じる抵抗)が増加する。それらのバランスによって最適値が決まる。
|
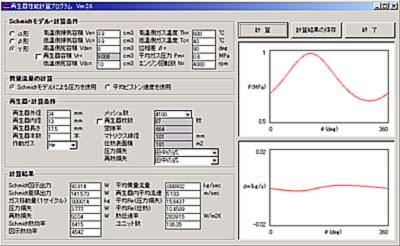
図9.10 再生器の設計計算画面
(画面をクリックすると大きい画像が表示されます)
|
(4) ピストン駆動機構
ピストン駆動機構には図9.11に示すロンビック機構を採用した(図6.28,図6.29参照)。ロンビック機構は、2つの歯車,ヨークおよび4本の連接棒で構成されており,図中の連接棒長さL、クランクアーム長さRおよび偏りeを適切に設定することで,直線上に配置したディスプレーサとパワーピストンとに90°程度の位相差を設けることができる。理想的に組み立てられれば、両ピストンは厳正直線運動を行う。しかし、組立精度が十分でない場合、ディスプレーサ・ロッドおよびパワーピストンが傾くため,各ピストンにサイドスラストが生じ,摩擦損失が増大する。本エンジンでは,パワーピストンに図9.12に示すような回転可能な節を設けている。これにより,組立精度に対する逃げを確保できる。
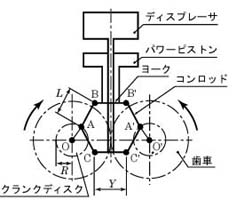
図9.11 ロンビック機構
|
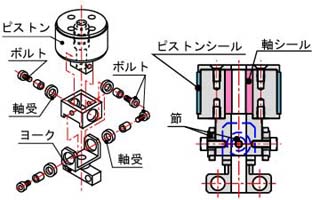
図9.12 パワーピストンの構造
|
(5) シール機構
本エンジンの主なシール装置には,ディスプレーサおよびパワーピストンのピストンリング,ディスプレーサ・ロッドのリップシール(往復動シール)がある。これらを選定する際には,機械損失を考慮したシミュレーションなどを利用した(図9.13)。その結果,ピストンリングにはPTFE製のエンドレスリング,ディスプレーサ・ロッドの往復動軸シールには,ガイドを兼ねたすべり軸受を用いた。また,通常のスターリングエンジンの場合,高圧の作動ガスの漏れを防ぐために出力軸端にメカニカルシールなどの回転軸シールを取り付ける必要がある。しかし,本エンジンでは発電機を圧力容器に内蔵することで,回転軸シールをなくし,摩擦損失の低減を図っている。
|
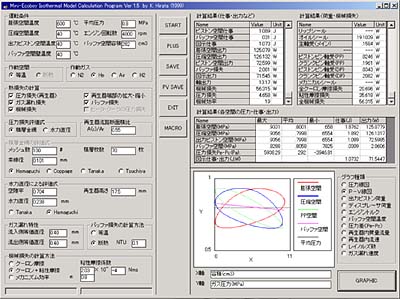
図9.13 機械損失を考慮したシミュレーション計算画面
(画面をクリックすると大きい画像が表示されます)
|
9.2.5 実験用小型スターリングエンジンの性能特性
エンジンを試作した後,様々な異なる形式の熱交換器や異なる形状のピストンシールやピストン駆動機構の部品を試作し,実験を行ってきた。現在でも実験を継続中であるが,目標性能には至っていない。
図9.14は,エンジン回転数に対する出力および機械損失の実験結果である。これより,最高軸出力は,エンジン回転数が約1100 pmで8 W程度であり,これは目標軸出力の50 Wに全く至らない結果である。主な原因としては,エンジン回転数が設計時の回転数の4000 rpmに比べてかなり低いことである。エンジン回転数を高めるためには機械損失の低減が必要不可欠である。
|
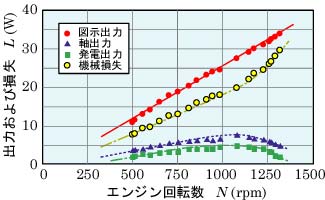
図9.14 出力および機械損失の実験結果
|
図9.15はエンジン回転数と各効率との関係を示している。これより,熱源効率(=有効熱入力/全入熱量)および発電機効率(=発電出力/軸出力)が約60%であるのに対し,図示効率(=図示出力/有効熱入力)および機械効率(=軸出力/図示出力)は10〜30%とかなり低いことがわかる。図示効率を上昇させるためには,熱伝導が小さいシリンダ(熱交換器)の開発が必要である。また,機械効率を上昇させるためには,機械損失の低減が必要である。
|
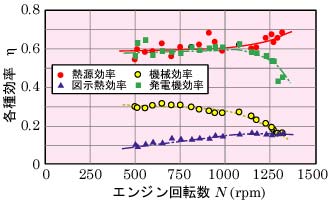
図9.15 エンジン回転数と各効率との関係
|
9.2.6 まとめ
以上,実験用スターリングエンジンの設計例を紹介した。一つのエンジンを完成させるためには多くの検討事項があり,多くの設計計算が必要であることを理解していただけたであろう。しかし,実験結果からもわかるように,設計計算の結果が必ずしも実際の機械の性能に一致するとは限らない。機械設計を成功させるためには,詳細な解析や性能評価が必要である。
|